Moving printing machinery since 1966
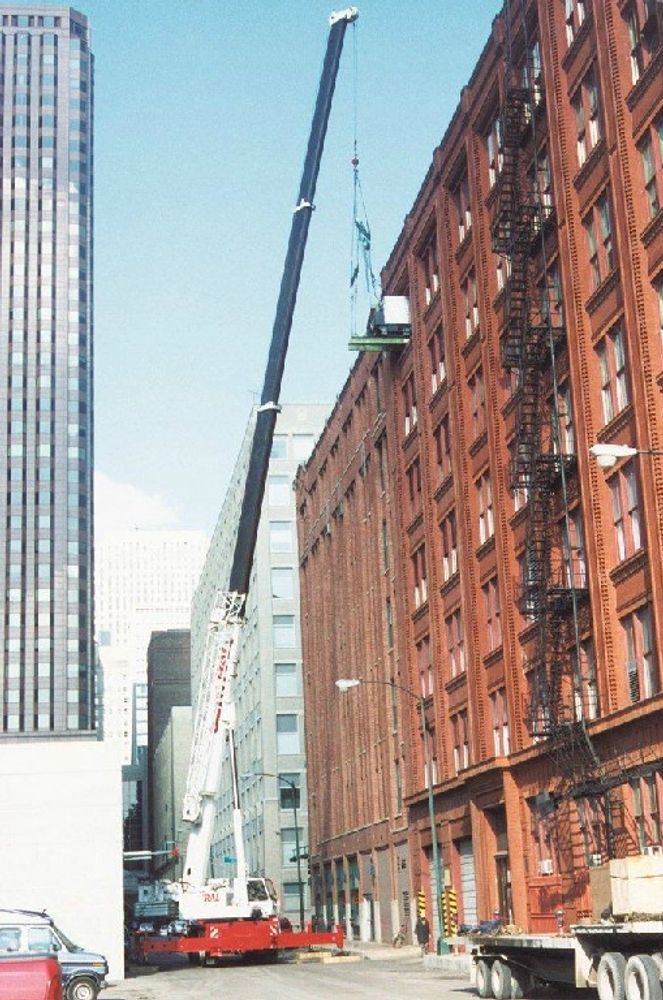
Ed Regan Sr. (219) 869-6400
Ed Regan Jr. (219) 866-5500
2499 N. 900 W. Rensselaer, Indiana 47978, United States
Master Riggers & Problem Solvers
I AM THE SENIOR ACTIVE FOUNDING OWNER MASTER RIGGER OF PRINTING MACHINERY IN THE USA
IT ALL STARTED IN 1966!
I was 16 years old, with no job. A high school buddy tipped me off that a fellow worker would quit at 2:30, and if I were there at 3:00, the owner would indeed hire me, as the shop was bustling. I arrived at this time with work clothes on. I was hired and immediately started work.
This was my first real job as a letterpress printer. Hand setting foundry printer's lead type into composing sticks. Locking up chases with quoins and keys, cutting paper, setting up and operating a 10 x 15 Heidelberg "windmill," Miehle Verticle, and a C & P hand-fed printing press, enjoying the addicting smells of a vintage print shop at Fancher Printers in South Holland, IL. This job was all part-time work while I was still in high school. I also took phone calls for customers' orders for their printing jobs, wrapped finished jobs, and made their deliveries as well.
I operated a sizeable Nu-Arc camera, exposing & developing the film, usually to a medium four on the grayscale. Then air dring the negative film on cloth line with old fashioned household cloth pins. Taking the dry negative and taping it to special stripping paper. Opaquing pinholes and scratching off unwanted dots, plus cleaning up other errors. Placing the corrected negative onto an old-style additive plate and exposing it in a Nu-Arc carbon arc vacuum frame, and then rubbing the red developer to bring the image up onto the printing plate to the desired look. I then mounted the plate onto the ATF Cheif 15, 1250 Multilith, 17 x 22 ATF Cheif / Webendorfer offset press & a Miehle / Roland 29" offset press.
This company is still in business today, owned by the late Donald K. Little and ran by son and daughter Ken and Susan.
I also moonlighted at other printers, simultaneously, The Wilson Press & Mr. G Printing Co., where I operated a Heidelberg cylinder letterpress, Ludlow, Linotype, Linograph & Elrod.
ALSO, IN 1966!
I saw an ad in the local shopper weekly newspaper that an elderly gentleman (maybe 80 yrs. old) had listed an advertisement that read "Complete hobby print shop for sale $225.00." The shop included an 8 x 12 Chandler & Price platen printing press, a small Challenge lever paper cutter, a granite chase lockup imposing table. Plus, all of the necessary ancillary items such as a furniture rack, quoins & keys, slug cutter, double wood bank of foundry type in California job cases, paper inventory, slug cutter, line gauges, ink, and so forth.
Everything that a beginner's start-up letterpress print shop would need. I found this gem of a shop located in a 100 yr. Old house. Down a winding outdoor stairway into a basement on the south side of Chicago, IL. I had to completely dismantle this press & cutter to fit them out of the doorway and moved everything out using a U-Haul truck by myself. I moved the shop into my mother's then 7 yr. - old, "new" tri-level house. (My parents bought the house brand new in 1959. My dad passed in 1963.)
I moved all of the equipment down the winding indoor stairway at this location also, and into the basement's furnace room and re-assembled everything. I set everything up and began printing, doing small odd jobs. I was very proud of my new print shop, now in Dolton, IL.
In 1967, in High school.
With one choice for an Industrial class, I picked the print shop, 50-minute class. Well, it didn't take very long for the shop teacher to develop an intense dislike for me. Evidentially he didn't appreciate the fact that I had already worked in a print shop & I also owned one. Perhaps he formed an opinion that I was a Mr. know it all? Who knows. I was the only student that could do "homework."
I had zero experience with silkscreen work. On my first ever try, I produced a seven-color job, in register with gold glitter sprinkles on the wet yellow paint. I received a C. Should have been an A+! (which I still have wrapped up in original 1967 wrapping paper) safely preserved. On all weekly exams, I had received 100%. The final grade for the year was an A. Deportment was a D. I was altho not among the disrupters whipping around lead type, hitting other students in the back of the head. I was very well behaved and deserved an A for this as well.
Then, realizing that I could move printing presses, I began advertising my services in the Sunday edition of the Chicago Tribune. In the sports section under the column headed "Printing Equipment & Supplies." The ad read, "Specializing in moving small printing presses" my name & phone #.
I started receiving calls almost immediately. I began doing small jobs on the weekends while maintaining my job at Fancher Printers during the week. I moved 10 x 15 windmills, Miehle Verticals, Kluges, C & P's, lever and power paper cutters, ATF Chief 15's & 17's, 1250 Multiliths, AB Dicks, light tables, Nu-Arc cameras, Baum & Cleveland folders, and other equipment with U-Haul trucks.
In 1968, a Great Year.
My late wife, Patricia & I were married. Our first two children were both born this year, not twins, but Irish twins!
Then in 1971.
We bought our 1st truck. It was a 1953 Ford F-350, 1-ton pick-up truck with a Flathead V-8 engine. We equipped it with a winch and wagon planks in the garage of our first new house in Steger, IL. I continued doing part-time jobs on the weekends, moving small printing presses, folders & paper cutters.
And in 1972.
I bought my first real heavy-duty truck. It was a 1964 IHC Loadstar (with butterfly hoods) 14 ft. long flatbed, equipped with a 30,000 lb. Catapillar winch, wagon planks hooked to the rear, w/old style cribbing used to brace-up the ramps.
I purchased it from Earl E. Bremer of EBCO Co. This small but very stout truck was perfect for negotiating the very narrow streets and tight turns in the crowded Chicago's downtown. I could quickly load 10,000 lbs. on it with no problem.
Earl was very talented ( Jack-of-all-trades ). I learned a lot from Earl, him being 26 yrs. My senior. He was a linotype, printing press, paper cutter, and an all-around mechanic & machinery mover. He taught me a lot about rigging elevators and craning machinery in or out of windows. He worked for me on a part-time sub-contractor basis, on and off for 9 or 10 years.
A couple of very weathered old polaroids of this truck are in the pictures section.
1974 was a monumental year.
By this time, I had built up a following of repeat customers. Probably over 200 or so. One of them was Tompkins Printing Equipment, at 712 S. Clark St., Chicago, IL. ( located in the center of the once-thriving & historic printer's row area of Chicago ). In the spring of 1974, I asked Mr. Larry Tompkins if he would provide me with an adequate work volume to justify my switching professions from being a printer to become a printing machinery mover. He agreed as long as I continued with the current quality of my work. I consider this the turning point for me to completely stop printing and devote all of my effort & energy to moving printing equipment.
Another big step in 1974.
I signed an industrial lease for a 3,000 sq. ft. warehouse with a truck high loading dock and a large DID. It had a friendly, air-conditioned, carpeted & tiled office in a brand new building in Dolton, IL. Industrial Park.
At the same time, in 1974.
I also approached both Mr. Henry Spero, owner of Type & Press of Illinois and Mr. Ed Stephens, owner of Jack Beall Vertical Service. I was doing a very considerable amount of their work, maybe 80%, for both of these companies plus working for Tompkins as well. So, being way before the invention of the cell phones were even thought of if someone needed to get in touch with me for an emergency, they could call one, or all three of the above & chances were very good that one of them would know where I was at any given time.
More in 1974.
My wife Patricia & I then picked out a lot (that was then a horse farm) in an original and the only culdesac in Dolton, Il., Diekman Ct. We had a charming Chicago style bungalow built to our specifications. Mr. Tompkins kept true to his word, as I was moving something in or out of the 712 S. Clark St. location at least three days a week for the remaining decade of the '70s.
Then in 1975.
I bought two semi-tractors & trailers: several larger forklift trucks, gantries, and other rigging tools and small machining equipment. The business was now really growing at a fast rate.
Then by the late '70s.
I had become increasingly involved in moving large format Harris sheet-fed & full size M-1000 heat-set web offset printing presses. I started working with a former Harris printing press erector named Joseph Yukich, who began working for The Harris Corp. in 1958. Mr. Yuckich's specific job was to erect, install, demonstrate and troubleshoot, large format, unitized Harris printing presses such as 59", 60", 77" & 78" sheet-fed presses.
The Harris Corp. shut down their sheet-fed press division in 1975. Mr. Joseph Yukich then became involved in the web division and later formed his own company, Universal Printing Machinery (UPM). UPM became a significant customer of mine, having me move large-format sheet-fed & heat-set web presses nationwide, coast to coast to large carton houses.
Working with Joe led to being formally trained in erecting a printing press to factory specifications. Such as precision leveling to tolerances of .0005 per ft., aligning, and, most importantly, tramming between the plate cylinder bearers. To move one - 6 color 77" Harris press from point A to point B would require ten semi truckloads and take a minimum of 6 weeks to accomplish. I did these giant jobs until the early '80s.
I was then factory-trained directly by The Harris Corporation to erect new full-size, heat-set Heidelberg Harris web printing presses. I also moved double-wide (96" web) rotogravure presses into the mid-'70s. The demand for these old, large, 78" & 96" wide rotogravure & offset presses fell off dramatically. These presses were becoming obsolete compared to the newer, 40" Heidelberg Speedmaster, RMGT, Komori, KBA, Miehle/Roland, Man-Roland, Ryobi, Mitsubishi, Planeta, Goss Community newspaper, Heidelberg / Harris web, Harris M 1000 heat-set web, flexographic, and, other equally advanced presses.
We also moved Challenge, Polar, Saber, Perfecta, Pivano, Dextor Lawson, Harris Seybold, Prism, Schneider, Como, Shimanek & more long lost history paper cutters.
By this time, my three sons, Tim, Jack & Eddie, joined with me in the moving business.
Then in 1986.
The pinnacle of my career was beginning.
Whitcomb Enterprises, owned by Larry and Maryann Whitcomb, was Heidelberg's primary rigger in Illinois. Larry Whitcomb was doing all of Miehle, Komori, and Heidelberg's work. Heidelberg didn't like the situation of their primary rigger doing work for their competitors. Heidelberg had a new 6/C 40" Speedmaster press to deliver, but Whitcomb was tied up moving Komori's and Miehle's at the time. Larry told Heidelberg that he would put them on the waiting list and get to their press in a few weeks. The hunt for another primary replacement rigger was ON!
Mr. Rich Mix, a Heidelberg salesman at the time, and coincidently formally a Tompkins salesman, had the answer. In a group meeting, he said, "Hey, what about the kid that did Tompkins work on Clark street!" He also helped move them into their empty new building in Schiller Park, IL.
I then received a call from Heidelberg asking me if I was interested in being one of their riggers for the Chicago area, including the whole state of Illinois and the northern 1/4 of Indiana.
I would become a back-up "Primary Rigger", (Heidelberg's terminology for "New Equipment Only") for their current "primary rigger" Heidelberg gave me 12 jobs moving the smallest equipment in their line, such as 20" presses and 30" cutters.
After I had completed these 12 jobs, Heidelberg's Bob Tuley, VP of the central region, called me into his corporate office in Mt. Prospect, IL. Mr. Tuley informed me that Heidelberg had surveyed these customers about my performance and received positive reports from all. Mr.Tuley then asked me if I was confident in handling their
massive 40" presses.
I replied that I had been moving large format printing presses for the prior 15 years. Heidelberg then began sending me a full size, 40" new printing presses to deliver and assist their mechanics in the erection and installation.
1987.
I became Heidelberg's sole "Primary rigger." They always had other "Secondary riggers," removing old, used equipment to make way for the new installation.
1989.
I bought out Whitcomb Enterprises, complete with their accounts, telephone number, and a few of their employees.
1991.
I purchased the 24,000 sq. ft. building on 4 1/2 acres zoned open industrial in Rensselaer, IN. I am currently still in this building now, close to 30 years.
1994.
My daughter Tina bought out The Wilson Press & we moved it into my building, where she operated it for a short time. The specialty job that was crucial to the company went extinct.
1995.
Heidelberg gave me the entire state of Indiana. In addition to Illinois, which I already had. I could barely keep up with the demand for delivering Heidelberg presses fast enough. We were running three crews during the week. During peak times, such as the end of the calendar year and the end of Heidelberg's fiscal year, April 10 at that time. These busy peaks meant seven days long weeks. On the weekends, we were gearing up for Monday's deliveries. May, June and July were typically much slower. We did this schedule for 18 years.
2004.
Everything was drastically slowing down. Shortly after that, Heidelberg closed the Mt. Prospect, IL. office that dispatched me. Many people lost their jobs, including me.
In the '70s, '80s, & '90s,
There were about 1,000 printing companies within a 5-mile radius of Chicago's loop. If one would take into account the entire Chicago metropolitan area, there were approximately 3,500 printing companies. And more specifically, the old printer's row area being nearly 100% concentrated with printer's, bookbinders, engraving companies, envelope manufacturers, die cutters, ink companies, paper folders, typesetters, plate makers, paper supply houses, paper converting & other printing-related companies.
10 to 20 different companies could be in the same building and use the elevator to complete a given job without leaving the building. A substantial amount of equipment required craning in or out of an upper floor window, or rigged up or down an elevator shaft.
Rigging an elevator:
Depending on the situation, a rigger could take an 18 ft. long process camera track, sling it to the bottom of the elevator car. Or on other occasions where the weight was only slightly more than the car's rated capacity, a rigger could attach the rigging to the top of the elevator car and assist, usually not needed, but cheap insurance. Other times, a rigger could float the machine inside the elevator car, so it would never touch the floor. I have this recorded on DVD.
The worst-case scenario is that the piece is dimensionally too large for the car. This situation was making it necessary that the elevator should be above the work area. The rigger will then insert his own I beam through the brick wall on one side. And block up the beam on the floor about two or three levels above the machine's final destination floor, and provide the appropriate lifting chain hoist/s and pull up or down the shaft, not using the elevator for lifting the machine at all.
If you wanted to be a machinery mover in Chicago back in those days, you had to know how to rig elevators and crane machines through windows. It was a must-have skill to survive. Now the classic printer's row area does not have even one single printer left there. All of the buildings are condos now!
Craning in or out of a window:
It is naturally preferable to crane in or out of either an overhead door or double "barn door" situation. The floor level is flush to the outside of the building. Sometimes a desired section of the brick wall has to be totally removed and then after the job rebuilt to its original condition.
It is also required to have the machine travel over a window sill, plus remove a 100 yr-old radiator. Case in point, the exterior facade is made of irreplaceable terra cotta tiles. We did such a job in 1997, with a new 20,000 lb. Heidelberg SM 74 2-H, using a 110 ton Krupp crane, the press was 75 ft. off the ground level on the 600 S. block of LaSalle St., downtown Chicago with the Sears Tower in the background. I had two cameras filming everything on this job, at all angles, plus narration. One camera was up, and one camera down recorded by a professional video service on a large format VHS, then transferred to DVD. This job is the first picture on this website!
Considering the above.
I can make the following statement until someone in the USA corrects me.
I AM THE SENIOR ACTIVE FOUNDING OWNER MASTER RIGGER OF PRINTING MACHINERY IN THE USA
It is my opinion, the spring of 2001.
The printing industry had found itself in a position of having overcapacity of existing equipment, changing technology to digital printing, the downturn in the economy, and foreign importing of printed material. This environment produced the perfect storm for downsizing the printing industry.
In my travels, doing this work in 40 states, I have kept my eye out for old 19th-century antique printing press equipment over the years. Some rare old presses buried & covered up in some corner of an old printing office have somehow found their way onto my truck. I have accumulated a fine collection of these historic pieces.
We have spent the last 20 years, taking out many presses that we had previously installed new and shipped them to foreign countries.
We have the experience - 55 years - the know-how and are poised to do our part to make the printing industry healthy again in the USA.
Dismantle, Transport, Fabricate, Erect and Install One Piece or Entire Plants Proven Dependability
No Matter How You Add It up Regan Movers Is A Plus For Meeting All Of Your Business Needs
Copyright © 2021 Ed Regan Printing Machinery Movers - All Rights Reserved.
Powered by GoDaddy Website Builder